Why Pneumatic Cylinders Fail - and What to Do About It
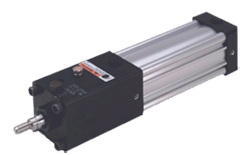
Ernie Lunski of Parker Hannifin Corporation wrote a great article on why pneumatic cylinders fail for MachineryLubrication.com. Below is an excerpt from his article.
Looking for trouble in all the right places
Whatever pneumatic cylinder system is specified for a particular application, the plant engineer can ensure optimal performance by knowing where to look for problems and observing appropriate troubleshooting protocols. New technical developments and increasingly sophisticated equipment refinements mandate a more focused troubleshooting effort for plant engineers to head off problems that can lead to downtime and equipment damage or failure. However, through a rigorous preventive maintenance and troubleshooting program and knowing where problems can come from, pneumatic cylinders can be kept running at optimum performance levels while maintaining maximum functionality.
Pneumatic cylinder failure typically results from five different conditions: side-load mounting, contamination, lack of lubrication, out-of-sync cycle rates and operation in excess of component limits.
1 – Side-load mounting
Because the function of a valve is to shift, the critical assessment of its efficiency is not when its position is stationary, but when it shifts. To ensure maximum operating performance, piston rod side-load mounting should be avoided because cylinders are specifically designed for push-pull stroke action. Due to the nature of side-load mounting, in which pivot mounts travel in an arc motion profile, problems can occur as a result of misalignment, off-center loads, rod deflections, imprecise tie-rod torque or long stroke action.
Side-load applications do not allow the piston rod to work in-line during the extend-retract motion of the cylinder. This can result in excessive seal failure, bushing wear or galling of the piston rod. In cases of catastrophic failure, bending of the piston rod or complete breakage of the rod can occur.
During installation exercise care to properly align the load to be moved with the cylinder’s center line. Correct alignment of cylinder piston rod with its mating machine component should also be checked in both extended and retracted positions to ensure proper operation. Improper alignment will result in excessive rod gland and/or cylinder bore wear, which shortens cylinder life. Note that a cylinder may have a side load – even though the rod was in-line when the cylinder was first installed – due to wear of pivot pins or mounting bolts working loose during use.
A rule of thumb is to select a mounting method that absorbs force on the cylinder’s centerline. If the piston rod is loaded primarily in compression mode, a better alternative is to select a cap-end mounting style. On the other hand, if the piston rod is loaded primarily in tension, a head-end mounting is the preferred best practice. In either case, all cylinder mountings should be checked on a regular basis.
Rod 'run-out,’ or deflection, is a measurement of the rod’s dynamic motion as it travels back and forth on its stroke. One method of determining rod deflection is to mount an indicator, run the cylinder full cycle and take indicator readings. The amount of rod deflection depends wholly on the cylinder’s alignment. Several installation options are available to optimize cylinder performance. These include reducing rod-bearing stress by adding a stop tube, while another option consists of using a rod-alignment coupler to prevent rod deflection.
2 – Contaminants
Cylinders can be contaminated internally from the air supply or externally from the operating environment. Types of contamination include solids, water and oil. As an example of the potential adverse effects of contamination, solids such as particulates, pipe rust and scale and thread sealant debris can curtail seal life, plug orifices and damage surface finishes.
Solids:
Gritty environments can wreak havoc with pneumatic cylinder systems. Once any type of particulate penetrates a nose seal, it can embed itself in seals and bearings, turning them into virtual sandpaper. But the potential damage resulting from solids contamination can be significantly reduced by keeping manufacturers’ port plugs intact and in place until the system is actually fitted with piping. A second option is to thoroughly clean piping before connecting it to cylinder ports to remove chips, burrs and debris left over from threading and flaring operations.
When cylinders function in hostile operating environments where excessive heat, chemicals, paint or weld splatter are present, shields can be installed to prevent piston rod and rod-seal damage. Additional installation options include using a metallic wiper to remove larger particulates from the rod or adding a rod boot to ensure further protection. Improving air filtration is another option to enhance cylinder performance.
Water:
Water vapor is present in all compressed air applications, where it collects within components to block orifice flow-through, dilute pre-lubrication grease, adulterate airline lubricants, damage barrel or rod finish and freeze in cold weather. Installation options to reduce the deleterious effects of water vapor include using stainless-exercised steel rods and fasteners or by employing special coatings or epoxy paints.
Oils:
Another type of pneumatic cylinder contaminant consists of oils resulting from air compressor lubrication carryover or synthetic oils that are typically incompatible with air-line components. Such oils can cause seal swelling and orifice plugging. Again, plant engineers have the option of selecting seals that are compatible with oils used in the application to dramatically reduce the damaging effects of such contaminants.
3 – Insufficient lubrication
Catastrophic failure can also occur when cylinder seals have insufficient lubrication. High or fast cycle rates can generate unsustainable shock loads at the end of a stroke when the piston hits the end-cap, or seals can simply run dry from a lack of lubrication. Heat generated by the system could compromise component temperature limits. Whatever the reason for cylinder malfunction, steps can be taken to anticipate and prevent failure.
Potential solutions to lubrication-related problems include selecting a 'non-lube’ cylinder, adding a lubricator to the air-prep system or integrating an injection lube system. The specifier could also select an air-cushion cylinder option, add a shock absorber or lower system pressure via a regulator, if applicable to the system configuration. A final option in this case would be to add flow control to the cylinder, if high speed is not a major concern.
When properly selected, installed and maintained, cylinders should be leak-free. The fact is, however, that one or more performance criteria may not be up to spec and leakage can occur. For example, environmental conditions such as temperature, moisture content or dry versus lubed service affect the wear – thus leakage rate – of a dynamic seal valve.
Again, steps can be taken to anticipate and prevent potential problems. For example, if leakage occurs between the end-cap and barrel, check the tie-rod torque. If the torque is on spec, then the barrel seal should be replaced. When leakage occurs in the rod bushing area, rod seals should be replaced. Inside the cylinder, leakage beyond piston seals can cause sluggish movement or settling of the cylinder under load conditions. This occurs due to leakage of worn piston seals and/or rings. Replacement is the only solution.
4 – Operating over component limits
Operating a cylinder over pressure, load and/or energy limits can also cause the component’s failure. When cylinders run at overload capacity, seals are subjected to higher stress and friction rates. Rod ends bend or break, and actuators can come apart. If the system contains speed control or energy-absorbing devices, pressure spikes can also occur that are two to three times above normal system pressures.
Several solutions are available to resolve these mechanical issues. First, the operator should make sure rod accessories are firmly shouldered against it by threading all the way down or by using spacers or shims. Alternative solutions include either increasing rod-thread size or using a studded rod end.
5 – Tailor troubleshooting efforts
As long as the plant engineer, the operator and the maintenance staff know what to look for in terms of unit design, operation, maintenance and troubleshooting procedures, efficient, reliable and cost-effective processes can be ensured.
Some key questions come in handy as a reference guide in optimizing pneumatic cylinder performance. These include:
- Am I using fittings that actually add contamination? Rusted fittings connected to the cylinder can introduce particle contaminates.
- Do my filters need changing? Filter changes should be a standard maintenance protocol to effectively remove particulates.
- Am I using the right tools to install my cylinder properly? Using the wrong tools to install cylinders can cause damage.
- Why do I need to properly torque fasteners? This ensures that tie-rods are installed properly.
- Is the product warranty in effect? Maintenance workers should check to see if cylinder faults are covered by the manufacturer’s warranty.
Additional potential problems can arise from materials used in cylinder construction. For example, a stainless steel cylinder distinctly differs from a stainless-steel body cylinder. Kinetic energy can also come into play in performance equations. Miscalculating kinetic energy can literally shatter a cylinder.
Operating pressures constitute another consideration in achieving optimum cylinder performance. If pilot control pressure is too low, the control line may be too small or the metering choke valve could be malfunctioning. Knowing what to do, how to do it and when to do it – in accordance with protocols of best practice procedures – will keep equipment humming at peak performance.
Read the whole article here: http://www.machinerylubrication.com/Read/1742/why-air-cylinders-fail-(-what’s-to-be-done-about-it)
Posted by Marek Bobik