Choosing between rubber, metal and metal flex hose assemblies
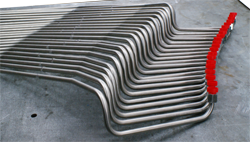
The purpose of this information is to help you determine what type of fluid lines are best for your application: metal tube assemblies (hard lines), rubber hose assemblies, or metal flex hose assemblies. Each has their strengths and weaknesses – read on to learn more.
Metal tube assemblies
Metal tube assemblies (sometimes called hard lines) are fabricated by cutting and bending bulk tubing and attaching tube fittings at each end. Materials vary depending on availability and application, but most commonly used tubing is carbon steel and stainless steel. Other tube materials include copper, aluminum and nickel alloys.
Reasons to choose metal tube assemblies:
- Excellent heat dissipation
- Provides great flow
- Generally lighter weight than rubber hose assemblies
- Can handle pressures above 6,000 psi
- Generally outlasts rubber hose assemblies
- Generally less expensive than rubber or metal flex hose assemblies
- Smaller outside diameter than rubber hose assemblies for the same inside diameter result in better space efficiency
- Good chemical compatibility; excellent for stainless steel tubing
- High heat resistance
- Tighter bend radius than rubber or metal flex hose
Reasons to consider alternative solutions:
- Flexibility is required
- High vibration applications
- Frequent replacement in the field due to equipment damage is expected, especially when spare tube assemblies are not readily available
- Exposure to moisture, especially salt water or other corrosive environments (unless stainless steel tubing, copper tubing or specially treated tubing is used)
Rubber hoses:
Rubber hose assemblies are fabricated by cutting the bulk hose to length and attaching the hose ends (sometimes called hose fittings) to either end by crimping, swaging or other methods (for field attachable and barb hose ends).
Reasons to use rubber hose assemblies:
- Generally easier to route a hose assembly over, under, around, or through a series of obstacles
- Generally easier to replace in the field
- Generally more widely available than either hard line or metal flex assembly
- Availability of wide range of hose types for wide range of applications
- Wide range of pressure ratings up to 10,000 psi
- Great resistance to vibration when used with proper fittings
Reasons to consider alternative solutions:
- Rubber hoses cannot withstand as much pressure and external forces as hard lines can.
- Rubber hoses are not as space efficient as hard lines.
- Rubber hose assemblies age and need to be periodically replaced.
Metal flex hose assemblies:
Metal flex hose assemblies are fabricated by welding the stem and butt of the hose ends together and welding the fittings onto the metal flex hose
Reasons to choose metal flex assemblies
- Need for the strength of a steel tube with the flexibly of a hose.
- Great heat resistance
- High pressure rating
Reasons to consider alternative solutions:
- Fabrication of metal flex hose assemblies involves welding the seam and butt as well as a fitting attachment. If not welded correctly, a leak path can be created.
- Metal flex assemblies are not readily available in most markets
A combination of the hard lines and flexible hoses can also be a great solution to unique challenges. It would be the most desirable combination if vibration is severe.
Posted by Joni Scott