Pneumatic systems - how to save money
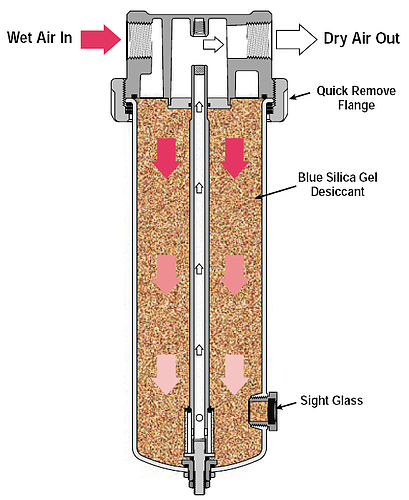
Save money on your pneumatic system.
If you have any moisture in your pneumatic system, you're losing money.
You’re probably saying “So what if there’s a little bit of moisture, my pneumatic system works just fine.” Although that is probably true, that moisture is slowly but surely doing (expensive) damage:
Effects of Moisture |
How each Costs you Money |
|
|
|
|
|
|
|
|
|
|
So how can I remove moisture from my pneumatic system and save money?
STEP 1 – First, ask yourself some key questions to determine your needs:
1. How much moisture is in your pneumatic system? Is there…
- Just a little water vapor? (May be OK for mechanical applications, but your pneumatic system would benefit from dryer air)
- Sizeable droplets? (You should address the moisture issue soon)
- Flowing water running through the lines? (You should address the moisture issue now)
2. How crucial is the absence of moisture to your application?
- Not a big deal, just trying to save money?
- A necessary safety precaution (moisture critical)?
Once your level of dryness has been evaluated, perhaps even a target dew point established, there are many solutions available. For pneumatic systems just trying to save a little money, the following solutions can remove vapor or droplets:
- Particulate filters
- Coalescing filters
- Bulk liquid separators
- Drip leg drains
Pneumatic applications that are moisture critical include Medical, paint, and semi-conductor. Repercussions of even a slight amount of moisture are much greater than in a mechanical application. Removing the vast majority (less than 100%) of moisture in a mechanical application might be sufficient, but it could spell disaster in some scenarios.
For pneumatic applications requiring the driest air, the following solutions can remove water vapor resulting in dew points as low as -100F (really low):
- Desiccant dryers
- Small refrigerant dryers
STEP 2- Install the pneumatic solution that best fits your needs.
Install your solution as close to your pneumatic application as possible to ensure the air being used doesn’t travel through any other elements. If you install the dryer at the compressor (far away from the application), there is still a chance moisture could develop in your pneumatic system further down the line. For example, moisture could develop if the lines are routed through environments that vary in temperature. Temperature variation induces condensation even after the air has been dried from the initial compressor. The best solution is to install a dryer as close to the end application as possible, or add additional dryers along the way. This will minimize the damage to your components, and keep more money in your pocket by prolonging the life of your pneumatic system.
More tips on saving money with pneumatic filters and regulators:
Posted by Vince Lockwood