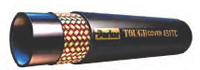
Wire Braid Reinforcement vs. Wire Spiral Reinforcement
- What’s the difference?
- Why should you care?
Each style of hydraulic-hose wire-reinforcement has its advantages:
Wire Braid Reinforcement |
Wire Spiral Reinforcement |
Hoses typically offer more flexibility |
Hoses typically offer more strength |
Wire Braid Reinforcement of Hydraulic Hoses
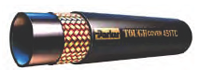
As you may guess from the description – or see from the image of Parker 451TC hose (left) – steel wires are braided together to create a flexible reinforcement layer. The advantage of wire-braid reinforcement is its flexibility. Hoses using this method of wire reinforcement typically feature a tighter minimum bend radius, and require less force to bend than their spiral-reinforced counterparts. This option, however, has one main disadvantage – it does not perform well in high-impulse applications. When a hose is pressurized, it expands in diameter (and gets shorter at the same time). When this happens, the braided wires rub against each other with great force.
So although wire-braid reinforcement results in a more flexible hose, the hose is also more susceptible to failure under high-impulse applications.
High-impulse applications are better served by wire-spiral reinforced hydraulic hoses.
Wire Spiral Reinforcement of Hydraulic Hoses
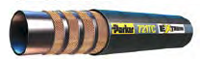
As opposed to the wires in wire-braid reinforcement, spiral hose reinforcement wires do not cross over one another. This helps alleviate excessive friction due to expansion/contraction during the pressure on/off cycle. The tradeoff is that hoses with a spiral reinforcement layer are typically harder to bend, because the wires cannot move within the layer as easily compared to braided wire.
So although wire-spiral reinforcement results in a stronger hose, there is also an increased minimum bend radius and more stiffness, which translate to decreased flexibility.
There are some exceptions to spiral hose inflexibility which take advantage of new technologies to overcome this decades old dilemma. Parker hoses 787TC and 797TC will be stocked by Motion & Flow Control Products, Inc. soon.
Posted by Marek Bobik