How do You Choose a Structural Adhesive?
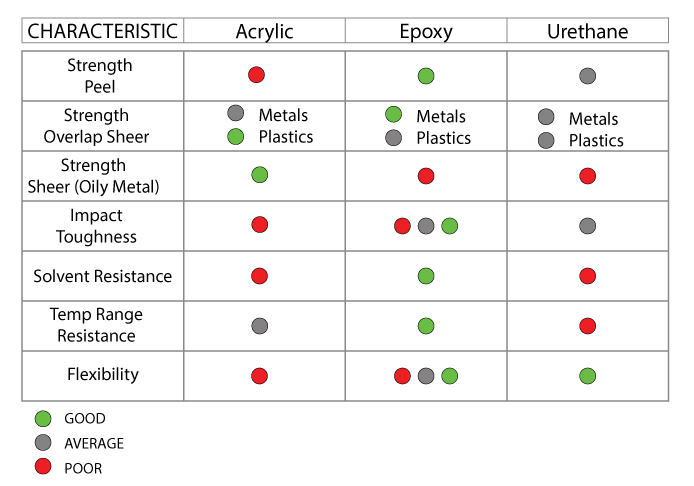
Structural adhesives offer many advantages over traditional bonding methods such as riveting, welding, or taping.
Improved Manufacturing Process:- Often no need for prep or finishing operations
- A wide range of chemistries, cure times, & viscosities accommodates countless manufacturing processes
- No heat distortion like with welding
- No concentration of stress at a joint location like with screws, bolts, or rivets
- Able to join dissimilar metals without risk of galvanic corrosion
- Excellent chemical & environmental resistance
- Generally, without protrusions, the product looks better
Selecting the Best Solution for Your Product & Manufacturing Process
Talking to an expert about your requirements is the safest bet, but it is always good to educate yourself on the topic before you do.
We can break down the structural adhesive selection into a four-step process: 1 – understand your application performance requirements; 2 – select the best category (chemistry) of adhesive based on the application; 3 – narrow down the choice based on the exact performance requirements and manufacturing process considerations; and 4 – test the limited number of alternatives before going to production.
Step 1: Identify the Performance Needs
The first step is to identify the performance needs of your finished products and the requirements and limitations of your manufacturing process.
For the product requirements, consider the following:
- Materials to be bonded
- The required strength of the bond and types of stress
- Vibration/shock
- Environmental conditions your product will work in or be exposed to
- Temperature range
- Moisture
- UV Exposure
- Exposure to chemicals
- Contact with food or beverages
- Sensitivity to off-gassing,
For the manufacturing process, consider the following:
- Required cure time to match the time it takes to apply the adhesive
- The temperature at which the adhesive will be applied and cured
- Application method – manual or robotic
- Storage conditions and shelf life
Step 2: Select the Chemistry
Specific adhesives can be somewhat tailored to the application. For example, add thickeners or thinners to increase or decrease viscosity, add accelerators to decrease cure time, or add a toughening agent to increase fatigue resistance.
However, the chemistry of the adhesive (typically classified as acrylic, epoxy, urethane, or cyanoacrylate – although they are hybrids) is the most significant determinant of the fitness for your application. The table below compares the properties of the epoxies, acrylics, urethanes, and cyanoacrylates.
Use the information to narrow down which chemistry is best suited for your product.
Epoxies
- Widest range of properties
- Best overall bond strength on metals
- Good vibration/impact resistance (except five-minute rigid epoxies)
- Perform well in temperature extremes
- Good choice for applications needing to flex or bend
- Require thorough removal of oils from metal joint surfaces
Acrylics
- Highest bonding strength on plastic
- Good bonding strength on metals, including oily metals
- Lower vibration/impact resistance than epoxies, which translates to lower fatigue resistance and temperature extremes
Urethanes
- Flexible
- Bond well to plastics, woods, and metals
- Most economical structural adhesives
- Lower strength, especially in higher temperatures
Cyanoacrylates
- Good shear strength on plastics and rubbers, but primers may be required
- Rigid and not well-suited impact applications, or where resistance to peel is needed
Step 3: Narrow Down the Choice
This is where more detailed analysis comes into play, and it is an excellent time to involve your vendor in your selection process.
First, you will need to dive into spec sheets to compile a list of suitable adhesives based on your specific bonding performance requirements. Once you have a list based on performance criteria, consider your manufacturing process, handling/storage requirements, and shelf life of adhesives.
Depending on your application, you may need to consider the trade-off between the ease of application and handling and processing.
Room Temperature Storage
Two-part epoxies are most stable, followed by acrylics. Urethanes have the shortest shelf life at room temperature and are sensitive to moisture in the air.
Cure Time
Two-part adhesives require time to cure after mating the parts – you need to clamp them until the adhesive sets. This slows the manufacturing process, but the extra time allows for positioning. Consult the manufacturers’ spec sheets for set times.
The two-part adhesive cure times are also temperature-dependent. They will cure faster in warmer temperatures and slower in cooler temperatures. Manufacturers typically list cure times at room temperature (about 70°F). The rule of the thumb is that the adhesives will cure twice as fast at 88°F, and take twice as long to cure at 52°F.
Viscosity Dependance on Temperature
Adhesives typically thin in warmer temperatures and thicken in cooler temperatures, but you can also select viscosity to match your assembly needs. Two-part epoxies and urethanes come in the broadest viscosity range options.
Offgassing
Some adhesives contain volatile organic chemical components or other components that can emit odors. Some can also cause skin or respiratory irritation. Before using any adhesive, consult the manufacturer-provided Safety Data Sheet and follow all precautions.
Epoxies – One-Part versus Two-Part
If you decided in Step 2 that epoxies best suit your need, you may need to look at the differences between one-part and two-part epoxies.
One-part epoxies generally provide the highest shear strengths on metal and resistance to high temperatures and solvents. Because they come pre-mixed, there is no need to measure and mix curative and base before application. The trade-off is that one-part epoxies are prone to premature aging and have cold temperature storage requirements. They also require high-temp curing at temperatures up to 350°F.
Contrast this with two-part epoxies, which must be carefully measured and mixed but are easy to dispense and do not require temperature-controlled storage.
Cyanoacrylates Considerations
Cyanoacrylates do not require mixing and have long pot lives. However, they can be temperature sensitive, and they cannot be repositioned once bonded, which may be an issue in some situations. They are also prone to blooming, so the whitish or rainbow haze along the bond line may not be acceptable where aesthetics are essential.
Following the first three selection steps should produce a list of a few adhesives to test.
Step 4: Test
For a final selection, however, conduct testing. You cannot rely solely on manufacturers’ spec sheets to make your final determination.
Typically, peel tests and overlap shear tests determine the strength of the adhesive on particular substrates or under specific environmental conditions. Design your test to reflect the conditions of your project. If you are supplying parts to your customer, consider testing your parts in their final assembly.
Our experts will work with you to choose and test the solution for your product. We can also involve LORD structural adhesive engineers to help you design or adjust your manufacturing process for the best results and efficiency.
Resources
- LORD Adhesive Selection Tool - use to generate a list of adhesives to evaluate based on materials you are bonding, and the application