Comparison of Alternative Actuating Systems: Electromechanical vs. Hydraulic vs. Hybrid
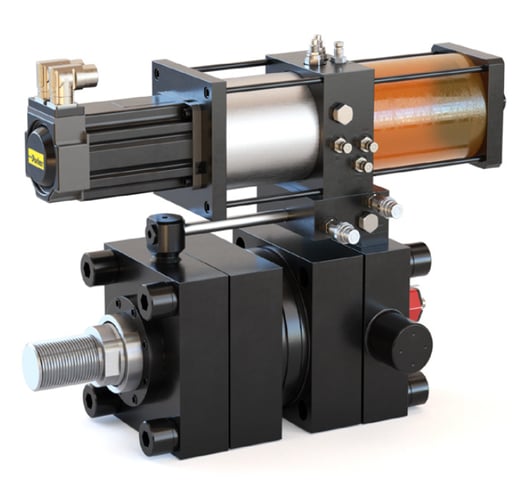
Electromechanical (EM) actuating systems have been increasing in popularity for some time. They have replaced pneumatic and hydraulic systems in many light-duty applications. Today,another option (such as the Parker HAS 500) is available: a hybrid of EM and hydraulic actuation systems, which combines the best of both worlds.
Below we will compare EM and hydraulic systems and take a quick look at the new hybrid system.
Electromechanical Actuating Systems
In a typical EM system, the motor is attached to a screw, with the actuator's rod connected to the nut. As the screw turns, the nut causes the rod to extend and retract. The lead screw transfers the small rotational force to the nut, converting the rotational energy to linear movement, and magnifying the force over a long distance. This enables moving a heavy load to over a small distance.
The biggest advantage of the EM systems is their relative simplicity; with EM, a single component, an electric motor, controls speed, direction, and thrust. Both hydraulic and pneumatic systems need to use multiple components to facilitate those same functions. Lower power consumption and environmental concerns of potential hydraulic fluid leaks are also cited as factors for choosing an EM system.
However, sliding motion screw type EM actuators have a limited service life due to metal to metal contacts with large amounts of friction between the nut and screw. That design aspect causes their efficiencies to be as low as 10-40%. The friction also creates heat, which adds its own set of challenges, and leads to unpredictable service life. Sliding motion screw type actuators are limited to light duty, intermittent applications. Rolling motion screw designs can achieve an efficiency of over 90%, and life expectancy of the screw drive assembly is easier to predict than in the sliding motion screw type systems.
Selection of the proper actuator depends on the load and motion profile along with expected number of cycles and requires expertise. EM systems are very application specific, and changes to the system can be complicated. They must be routinely lubricated; stroke, screw speed, frequency, and lubrication type all have an effect on the life of the system. Finally, EM actuating systems are very rigid, which makes them prone to excessive wear and damage from vibrations and shock.
Hydraulic Actuating Systems
Traditional hydraulic systems consist of a directional control valve to manage direction, a flow control valve to regulate speed, and either relief valve or pressure control valve to manage actuator thrust. Another typical setup involves using a proportional valve in place of the directional and flow control valves. However, that solution creates pressure loss and generates more heat, which in turn creates a need for an addition of a heat exchanger. With the use of proportional valve and heat exchanger, the whole system becomes less efficient.
Hydraulic fluid provides continuous lubrication to the components of the system, which limits wear and tear, and reduces friction between moving parts. As a result, hydraulic cylinders and valves have a very long service life and an exceptionally high level of efficiency. The hydraulic fluid also has a dampening effect, so hydraulic systems are better able to withstand vibration and tolerate shock.
As is the case with EM systems, setting up a hydraulic system requires expertise, plus when a component fails, identifying the failed component in a complex system can be a tricky task, even for an experienced hydraulics technician.
Hybrid Actuating Systems
The latest evolution in actuation is Hybrid Actuation System (HAS) combines the benefits of electromechanical systems with the proven reliability and high-power capacity of hydraulic systems. HAS uses an electric motor for power, which turns a hydraulic pump, which in turn uses fluid motion to actuate a hydraulic cylinder. Utilizing a hydraulic cylinder to perform mechanical work results in a 300% higher power density over what could be achieved by a comparably sized EM actuator.
The HAS does not suffer from mechanical wear and tear typically associated with the EM systems. Using HAS eliminates the burden of dealing with multiple components at multiple locations, connected by hoses, tubes, and adapters - all of which create additional opportunities for failure, more leak points, added maintenance requirements, while also making system troubleshooting more complex.
Parker HAS 500
Parker has been testing their plug-and-play hybrid actuator system since 2016, as mentioned in the Hydraulics & Pneumatics Magazine article from May 13, 2016. Today, the HAS 500 system is a high force, self-contained linear actuation system that is easy to position wherever the work needs to get done. It has the look and feel of an electrical actuator, but the power density and fail-safe characteristics associated with traditional hydraulic systems.
- Easy to Install
- Easy to Set Up
- Easy to Operate
- Serial bus connectivity, network connectivity
- Local discrete operation
- The sealed system keeps external contaminants out, and does not limit the orientation of the actuator
- Reservoir volume of less than 1 gallon
- The oil is pre-flushed and cleaned for a worry-free operation
- The integral filter allows for maintenance-free operation (up to 8000 hours)
- No fittings, hoses, or other connectors required
- Integral flow tubes with elastomeric seals ensure leak-free operation
- Compact brushless permanent magnet motors provide power on-demand in a small envelope
- Choice of pre-programmed drives with multiple serial bus communications, or simple local discrete operation
- Proportional speed, and directional control standard
- Optional highly sensitive system monitoring system detects and diagnoses potential malfunctions and maintenance issues before they can disrupt operations
By integrating a highly engineered compact power source into a hydraulic cylinder, this Parker design eliminates the time and cost associated with hydraulic power units, hydraulic hoses, fittings and fluid requirements for a traditional valve actuator. The hybrid EM/hydraulic system provides the robustness, power density, and fail-safe operation of traditional hydraulics with the ease of control using electromechanical actuators in a self-contained plug and play package.
Like EM solutions, the Parker Cylinder Division HAS technology localized power allows for improved energy efficiency. This is due to the elimination of the directional and flow control valving as well as locating the pump on the actuator, which reduces the amount of wasted energy commonly found on traditional hydraulic systems by 25%.
HAS 500 systems feature an integral sealed oil reservoir, which makes the system extremely resilient in contaminated environments. The reservoir expands and contracts to accommodate changes in volume and pressure. It does not "breathe" like oil reservoirs in traditional hydraulic systems, so there is no way for airborne contaminants and moisture to enter.
The sealed reservoir shell is available in steel, aluminum or composite material, allowing for a water-resistant barrier. The reservoir contains an integral filter (tested for more than 8,000 hours of operation), that enables HAS-500 to operate maintenance-free with no need for a hydraulic fluid change. The sealed reservoir and other features enable integration into the harshest environments without the worry of ingesting contaminates, and continued operation with minimal maintenance requirements.
Finally, with the need for smart components, the HAS 500 offers an easy plug and play control package for both industrial and mobile applications. In industrial applications, HAS is available with a Parker AC890, matched pre-programmed drive kits. For mobile applications, a Parker IQAN compatible hardened and pre-programmed motor matching inverters are available, supplying up to eight modules per BUS in relation to speed and direction control with optional pressure limiting.
Has 500 systems are available with standard Parker cylinders series including the 2HB/3HB square head, 2HBX/3HBX square head electro-hydraulic, and the RDH round line series. This chart highlights the base
cylinder nomenclature and the new HAS nomenclature with call out for the cylinder series. As of the writing of this article, the lead time is 10 weeks. Request a Quote for pricing.
BASE CYLINDER P/N | HAS P/N |
---|---|
2HB | HS2 |
3HB | HS3 |
2HBX | HS2X |
3HBX | HS3X |
RDH | HSR |
HAS-500 IoT Connectivity
The Internet of Things is here, and HAS is getting ready for data monitoring, gathering, and analysis with the goal of continual production and process improvement. With localized control, plant managers and process engineers can now trend actuator efficiency and system throughput to maximize uptime. The potential exists to monitor not only direction, speed, and thrust, but wear thresholds for scheduled maintenance and component replacement. With IoT connectivity, downtime becomes predictable and productivity optimized. The possibilities for real-time interactivity will eventually extend to even the most complex heavy-duty applications, where bus network units enable engineers to retrieve and relay information with simple two-wire controls.