Choosing Between Hose and Tube Assembly for Hydraulic Systems
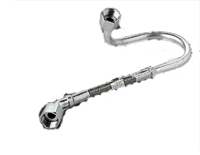
When choosing between a hose assembly and tube assembly for a hydraulic application, there are a few basic questions that must first be answered:
![]() |
|
![]() |
The short answer is that each has its advantages and draw-backs. One piece of hydraulic equipment will commonly have both tube and hose assemblies on it, depending on which solution better serves each particular part of the system. For example, tube would typically be better when routed close to a heat source, and hose would be chosen for high vibration applications or when attached to moving parts.
For the long answer, read on…
The table below outlines the most obvious differences. Some benefits of one solution line up neatly with disadvantages of the other, but not always:
Benefits of Tube
|
Limitations of Hose
|
Benefits of Hose
|
Limitations of Tube
|
Flexibility
Better Choice: Hose
![]() |
Even a small amount of movement of connected parts will rule out the use of tube assembly. Even if a tube assembly would initially work, the movement will put stress on end connections (causing a leak over time) and repeated movement will fatigue the tube itself. Either a hose or a hose-tube combination is the better way to go. |
Life Span
Better Choice: Tube (In most situations)
This is a general rule but it does not always apply – the effects of vibration, abrasion, exposure to chemicals, UV light, heat and other factors may either diminish the advantage of a tube assembly or even make a hose assembly the better choice. Tube will typically outlast a hose in applications involving exposure to UV light and high-cycle, high-impulse applications. Hose may outlast a tube if equipment experiences vibration.
These factors are discussed in more detail later in this blog.
Continuous Length Availability
Better Choice: Hose
The maximum length of an assembly is limited by the availability of hose or tubing in continuous lengths. Hose is usually available in much longer lengths than tubing. Some style of hoses can be produced in continuous lengths of 500' or more. By comparison, (hard) metal tubing material typically comes in 20' lengths. Longer tubing can be obtained but at increased cost and with longer lead time. Also, shipping and storing tube is more difficult, since it cannot be coiled like hose.
If long runs of tubing are needed, use tube fittings to join multiple tube assemblies together.
Expansion Under Pressure Consideration
Better Choice: Tube
When a hose is pressurized, its diameter expands and its length decreases. (When routing a hose assembly, make sure that it has enough slack so the hose does not pull out of the fitting under pressure.) Overall, the volume of the inside of the hose slightly increases under pressure. With enough hoses used in a system, the increase in the amount of hydraulic fluid necessary to complete the task can become noticeable and may need to be considered in the design stage.
In addition, the hose’s volume fluctuation decreases the hydraulic system reaction time and efficiency.
By comparison, the expansion of metal tube is negligible, which makes it a preferred choice for applications requiring accurate positioning.
Bend Radius Requirements
Better Choice: Tube, if a tight bend radius is required
Tube assemblies can have much tighter bends than hose assemblies. With that said, choosing a tight bend radius can increase flow resistance. While tubes can be bent using large radius blocks, producing tube assemblies with multiple bend radii is tricky and drives up cost and lead time. Most tube assemblies are produced using only one bend radius for the whole assembly.
With proper clamping, hose assemblies can be routed using multiple bend radii without problems (as long as the hose is not bent past its minimum allowable bend radius).
Abrasion Resistance
Better Choice: Tube
Even with abrasion resistant hose covers or sleeves, hose will likely suffer more than tube in highly abrasive environments.
Weight Consideration
Better Choice: Depends - review product specifications carefully if weight is important to your application.
When most people compare sizes of tubes and hoses, they compare nominal sizes, such as 1/2" tube with 1/2" hose. If you do that, you will find that in general, the steel or stainless steel tube will be lighter than a hose with the same NOMINAL size.
However, because hoses are measured by inside diameter (ID) and tubes are measured by outside diameter (OD), a tube will always have smaller diameter than a hose of the same NOMINAL size.
When sizing components for hydraulic systems, it is the ID dimension that is important to determine the flow diameter, flow velocity etc. So when you are considering which will be lighter in your application, you should compare tubes and hoses with the same diameter and required pressure rating instead of using nominal size.
When comparing tubes and hoses with similar ID and pressure rating, the weight difference often favors a hose - but not always.
For example, let's compare steel tubes and hoses with about 1/2" ID and at least 3,000 PSI rating.
Common steel tube sizes with about 1/2" ID:
OD |
Gage |
ID |
Weight |
C-1010 Steel |
5/8 |
.083 Wall |
0.459 |
0.4810 |
3,350 |
3/4 |
.095 Wall .120 Wall |
0.560 0.510 |
0.6646 0.8070 |
3,150 4,110 |
Note that in order to have around 1/2" ID with pressure rating at least 3,000 PSI, we need to look at nominal sizes of 5/8" or 3/4".
Parker hydraulic hoses with 1/2" ID:
Hose Style |
ID |
Weight |
Pressure Rating |
387-8 | 1/2 | 0.2900 | 3,000 |
487-8 | 1/2 | 0.3500 | 4,000 |
787-8 | 1/2 | 0.4500 | 5,000 |
797-8 | 1/2 | 0.4500 | 6,000 |
451-8 | 1/2 | 0.3500 | 3,000 |
302-8 | 1/2 | 0.4500 | 4,000 |
436-8 | 1/2 | 0.3400 | 3,500 |
BXX-8 | 1/2 | 0.4600 | 3,500 |
721-8 | 1/2 | 0.5400 | 4,000 |
M808 | 1/2 | 0.4600 | 4,000 |
Note that some hoses are lighter than steel tubes of similar inside diameter and pressure rating.
As you can see from the two tables above, depending on the style of hose used, it can be either heavier or lighter than a tube with a similar inside diameter and pressure rating. In some cases, the hose is not only lighter but it is rated to higher pressure.
On the other hand, C-1021 steel (more expensive) has a higher pressure rating, which means that a thinner wall (and smaller OD) tubing could be used, resulting in some weight reduction.
If weight is an important consideration for your design, make sure to compare the tube and hose specifications before making a decision and don't assume that the tube assembly is lighter.
Ease of Installation
Better Choice: Hose, in most cases
Hose assemblies can be "snaked through" tight spaces much easier than rigid tube assemblies. On the other hand, for the same ID, tube assemblies will have smaller OD, making it possible to fit them better to some places.
Availability and Ease of Fabrication
Better Choice: Hose, in most cases
Availability is related to ease of fabrication. In general, since hose assemblies are easier to fabricate, it makes them more available. It normally takes longer to set up a bender than it takes to fabricate a hose assembly.
Tube bending also requires special tools and trade skills that are less common than those required to fabricate a hose assembly. There are fewer sources for tube bending than hose fab.
However, if we are talking long production tube assembly runs, then the time it takes to engineer the tube and set up a bender gets spread out over a large number of assemblies – and the time it takes to fabricate a tube assembly as well as cost are greatly reduced. If produced in large enough quantities, a tube assembly can be more economical than a comparable hose assembly.
Vibration Considerations
Better Choice: Hose
Tubes do not typically perform well when exposed to continuous severe vibrations. Vibration fatigues the metal, leading to premature tube failure
Sometimes a short run of hose can be used to insulate the tube from effects of vibration.
Corrosion Resistance and Chemical Compatibility
Better Choice: Depends on the application
This is another area where careful research before deciding is paramount. Typically, a rubber cover protects hose’s metal reinforcement layers from corrosion – but hose ends are still susceptible to it. Use stainless steel hose fittings (or aluminum, if high pressure is not needed) and stainless steel tubing, if the assemblies are exposed to moisture, sea water, etc. Sometimes, painting the hose and tube assemblies is enough to keep rust at bay.
When considering the chemical compatibility of an assembly, each part needs to be considered separately. For hose assemblies, an inner tube material, cover material, hose fitting body material and seal material all need to be considered. For tube assemblies, both tubing material and tube fitting material need to be considered. Make sure that your assembly is compatible not only with the media conveyed but that it can withstand contact with chemicals in its intended environment.
If you cannot find parts that are made of material rated “Excellent” or at least “Good”, make sure that you adjust your maintenance program to include frequent checks and scheduled replacements of affected parts.
Chemical Compatibility Tables:
- Chemical Compatibility of Parker Rubber Hoses
- Chemical Compatibility of Parker Plastic Hoses
- Chemical Compatibility of Parker Plastic Tubing
Electrical Conductivity/Insulation
Better Choice: Depends on the application
Metal tube assemblies are electrically conductive but hose assemblies can be either conductive or non-conductive.
In most cases conductivity of a hose assembly is not an issue but in some cases it is extremely important. (Read our earlier blog, “Electrical Properties of Rubber Hose”.)
The only time you can be sure of the electrical conductivity (or non-conductivity) of a hose assembly is if the hose is specifically rated by the OEM as either conductive or non-conductive, or if you measure the conductivity yourself. For industrial hose assemblies, there is also a way to fabricate an electrically conductive industrial hose assembly by connecting the hose’s metal reinforcement to the hose ends.
Note on Galvanic Corrosion: Another consideration should be given to using different materials for tube and tube fittings, or connecting tube or hose fittings to ports made of different materials. To prevent galvanic corrosion, materials that are too far apart on metals corrosion scale should not touch. Refer to the Metals Corrosion Scale and Tube and Fitting Material Compatibility Chart for more information.
Heat Dissipation/Insulation
Better Choice: Depends on media and ambient temperature
If your system is overheating, using tube assemblies instead of hose assemblies can help dissipate heat better and help to cool the oil down a few degrees.
On the other hand, if your equipment is running in a cold environment, hose assemblies will better insulate the oil and help get the system up to operating temperature.
Resistance to the Effects of UV Light
Better Choice: Tube
Steel is unaffected by exposure to UV rays. Rubber compounds that are typically used in hose covers do break down over time from exposure to UV/sunlight. However, new compounds are being developed and some hoses are using specialized thermoplastic cover materials, which are UV resistant. UV resistant covers are still not UV proof but can withstand much longer exposures to UV before breaking down.
Temperature Ratings
Better Choice: Tube
Most hydraulic hoses are designed to work in temperatures between -40˚F to 212˚F. Low temperature and high temperature hoses are also available which can perform in temperatures as low as -70˚F and as high as 302˚F. However, the working pressure of a hose may be derated in some temperature ranges for certain media.
By comparison, carbon steel tubes can work in temperatures between -65˚F and 500˚F and stainless steel tubes can perform in temperatures between -425˚F and 1,200˚F. Temperature (and severity of service) derating factors still have to be considered when using metal tubing, but the derating occurs in much higher temperatures than is the case with hose. Please refer to Temperature Ratings for Common Tube Materials for more details.
Pressure/Vacuum Ratings
Better Choice: Depends on several factors
Each hose and each tube has a working pressure rating. For hoses, the pressure rating is typically noted on their layline but it is important to also check if the hose is derated for use at higher temperatures or with certain media. This information is typically available from the hose manufacturer.
For tubing, the pressure is typically dictated by the specifications that the tubes conform with. While it is also derated for service severity and high temperatures, tubing working pressure is derated in much higher temperatures. Please refer to Parker Tube Pressure Rating tables.
When considering a pressure rating of hose or tube assembly, the maximum working pressure is the lesser of the hose or tube pressure rating and pressure rating of fittings. The pressure rating of tube fittings, hose fittings, and adapters depends on size, material used, and end configuration. Smaller fittings will typically be rated to higher pressure. There is also a difference between the pressure ratings of JIC, O-Ring Face Seal, or Pipe fittings of the same size and material.
While many hoses are rated to 28 in Hg vacuum, most tube assemblies will outperform hose assemblies in vacuum rating.
Maintenance Considerations
Better Choice: Tube
Hoses typically have a shorter service life and often give no warning of failure, which makes them more demanding maintenance items in hydraulic (or pneumatic) systems.
Overall, if tube can be used, it will require less maintenance/replacements than hose and the cost of ownership over time is typically much less than a hose.
References:
Determining Tube Size for Hydraulic Systems (ihservice.com)
http://www.machinerylubrication.com/Read/25963/hydraulic-equipment-hose-tube