Small Oil Spill Can Cost More than You Think | Oil Spill Supplies
Written by Alicia Brimhall
9 min read
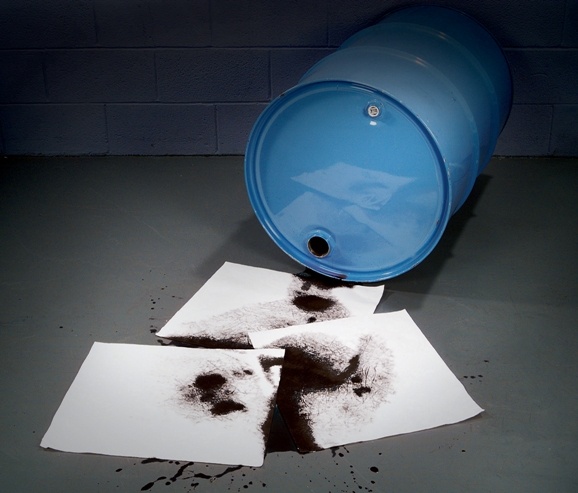
When people talk about oil spills, the first image to come to mind is often the large-scale disasters involving oil rigs, oil pipelines or derailed trains. Barrels of oil saturating the soil or dumped into a body of water, with devastating effects on the environment– this is a worst-case scenario come to life. The cost of a major spill, in dollars, man hours and damage to a company’s reputation, can be enormous. What you may not realize, however, is that spill containment on a smaller scale can be very costly as well.
Consider the following examples of actual cleanup costs incurred for spills in the Barataria-Terrebonne estuary area:
- A spill of two barrels (84 gallons of oil) cost the company $6,094 for labor and equipment. That comes to $72.55 per gallon.
- A spill of 8 gallons cost $41,717, or more than $5,000 per gallon.
- A spill of only 6/10 gallon (less than 5 pints) of oil cost the company $8,672.
Starting to see a pattern? Almost paradoxically, the very small spills in these examples cost the company far more per gallon than the largest spill. Labor costs in these examples include both the cost of the time that the company’s own personnel spent on the spill and the cost of outside personnel hired to assist in the cleanup, so securing labor and transporting to the site can still be costly regardless of the size. Spill clean-up expenses often also depend upon how much the oil has saturated, whether specialized equipment needs to be acquired, and many other factors. Even if a federal or state agency takes charge of the cleanup effort, the company at fault receives the bill once the site has been remediated.
It is important for companies to develop strategies for the prevention of spills and for keeping costs and damages to a minimum when they do happen.
Preventive Measures for the Operators of Hydraulic Machinery
Investing in preventive measures now can save your company thousands of dollars and headaches in the future. These preventive measures will not only help prevent oil and chemical spills, but will also prolong the working life of your equipment.
- Have a preventive maintenance program – and follow it. Maintain records indicating inspection dates, what was inspected, and by whom.
- Install monitoring equipment to track temperature, pressure and humidity at key locations on your equipment/machinery.
- Train personnel on how to spot a hydraulic hose that is nearing the end of its working life.
- Rubber hydraulic hoses and hose assemblies must be properly stored in order to function properly when installed. Did you know that the rubber hoses have an expiration date of 10 years from the manufacture date? Learn how to read the hose layline to determine the manufacturing date.
- Use non-spill couplers to connect attachments
- Train the personnel in emergency shut-down of your hydraulic equipment. Conduct practice drills if possible.
- Provide training for your personnel.
Oil Spill Containment and Clean-up
Even with preventive measures in place, spills do happen. OSHA standards require that any facility or vehicle working with hazardous materials such as hydraulic oil must be prepared for spill containment and removal. Some of their safety standards and recommendations include the following:
- Unused or expired equipment should be removed from your site.
- Infrequently used equipment should be periodically tested.
- Provide durable connections, as threaded connections tend to leak over time.
- Secondary devices such as gauges, meters, and valves should be located as close as possible to the primary connection point.
- Keep oil spill supplies nearby where hazardous materials are stored and could leak or spill. This includes work facilities, construction sites and trucks transporting hazardous liquids.
- When a small leak/drip is detected, immediately place an absorbent pad under the leaking connection.
- Prevent worker injury by quickly blocking off spills. Use diatomaceous earth, which has coarse granules that absorb and provide traction on slippery surfaces. Oil spill kits are commercially available and contain supplies needed for quick response to spills.
- Do not allow spills to reach storm drains or other drainage systems, as oil can contaminate water sources and threaten wildlife.
- Safely dispose of materials saturated by oil. Wearing gloves, use disposal bags, zip ties and air-tight sealable containers to ensure that any hazardous materials have been safely removed from the site.
Here are some prioritized steps to follow in case of oil spill:
- Wear protective gear
- Isolate the area
- Confine the spill
- Stop the spill
- Clean the spill
- Safely collect and contain materials saturated by the spilled substance.
- Wearing protective gear, use disposal bags, zip ties and air-tight sealable containers to ensure that any hazardous materials have been safely contained.
- Once done, use the same procedure to contain used protective gear.
- Dispose of the contaminated materials
- In some cases, the spill has to be recorded and/or reported to specific state agencies and EPA by phone. Check your local laws.
- Evaluate your response
- Is there something that could have prevented the spill in the first place?
- Were the company's procedures followed?
- Is more training needed in order to improve an outcome in case of a future spill?
- Were the company's procedures adequate?
- Can any changes be made to improve the current procedures?
- Set up training with any changes you have made. Substitute safe liquids to simulate hazardous materials that could be involved in any future spills.
Published Tue, Jun 02, 2015 @ 11:00 AM