Preventive Maintenance vs. Predictive Maintenance
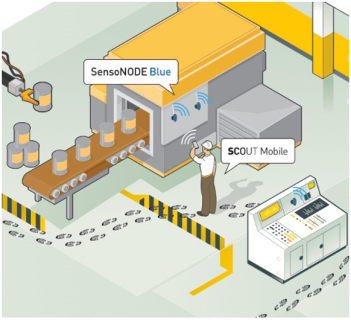
Author: Dan Davis, product sales manager, Parker Hannifin.
The terms Preventive maintenance and Predictive maintenance are often used interchangeably but are considerably different. Understanding the difference can help you come up with a better maintenance plan, and save you time and money in the long run.
Preventive Maintenance
Preventive Maintenance refers to the scheduled maintenance and servicing of equipment to keep it and in satisfactory operating condition. Preventive strategies include:
- Scheduled routine inspections
- Scheduled system tests
- Scheduled oil changes and lubrication
- Regular measurements and adjustments
- Scheduled parts replacement
- Record keeping of equipment deterioration
Preventive maintenance keeps to a set schedule, either determined by the manufacturer of the equipment or a company’s maintenance staff. Better than a “fix it when it breaks” approach, preventive maintenance helps prevent equipment failure by systematically replacing deteriorating components before they lead to failure.
While a maintenance schedule will help reduce unplanned downtime, it does little to reduce maintenance costs for labor and spare parts. Determining the ideal time to replace components is not an exact science, because it focuses on estimates rather than actual equipment condition, resulting in unnecessary work.
Often, this leads to the replacement of components prematurely and sometimes creates new problems. Studies show that 30 percent of PM is unnecessary, and another 30 percent can be harmful if a human error causes collateral damage, leading to additional downtime.
Predictive Maintenance
Predictive Maintenance improves on the idea of preventive maintenance replacing only parts that are about to break down instead of relying on a schedule. It saves time and money by performing maintenance only when it is necessary.
This approach minimizes unplanned downtime and reduces repair costs, including labor and part inventory. Employing a condition monitoring solution that tracks asset/system pressure, temperature, vibration, increased noise, humidity levels, and other conditions is the most effective predictive maintenance strategy because it covers three critical bases:
- Provides real-time and historical data trends of assets and processes.
- Allows operators to detect and diagnose any issues that could snowball into problems.
- Delivers analytics and alerts to operators when needed.
That last point is especially important. Condition monitoring for predictive maintenance gives operators the power to predict and improve processes, so they can optimize systems and assets based on what’s actually happening rather than simply reacting to unexpected events or "fixing" problems that may not even exist.
Predictive Maintenance Implementation
Slapping a sensor on every piece of equipment in your plant sounds like a nirvana of predictive maintenance, but applying a predictive maintenance solution to every asset in a facility just isn’t cost-efficient. Consider what’s practical before implementing a predictive maintenance solution. Give preference to assets and systems that are process-critical, expensive, or can cause collateral damage if they were to fail.
If failure of a particular asset or system will do little to no damage to the overall process, you can probably get away with a preventive, or even reactive, maintenance strategy (though we don’t recommend that last one).
A properly balanced predictive/preventive maintenance strategy will:
- Save labor costs exponentially.
- Allow for fast and precise diagnoses and identification of issues.
- Simplify the monitoring process; what once took hours will take minutes.
- Reduce troubleshooting time.
- Drastically reduce repair inventory.
- Increase process efficiency, maximizing throughput.
The good news
When used in tandem, Parker’s SensoNODE™ Blue sensors and Voice of the Machine™ mobile software provide an accurate and easy-to-use condition monitoring for predictive maintenance solution that uses Bluetooth technology to transmit data wirelessly.
Designed to work seamlessly together, SensoNODE Blue sensors and Voice of the Machine software allow less staff to quickly monitor more points of importance with increased accuracy, helping them cover more ground in the same amount of time, or even faster. Read more about the SensoNODE solution.
Source: Parker Hannifin Fluid Gas Handling Team